Constant monitoring and control of coffee vending machines is necessary to keep the vending machine making maximum profit. Without checking the equipment performance or providing proper maintenance in a timely manner, the machine will stand idle. In this article, we will share with you how the B2Field web-service and mobile app can ensure a smooth operation of the equipment and remote control of the operators.
According to the statistics, over 60% of all vending machines specialize in coffee drinks. After all, the margin of such machines ranges from 200 to 400 percent.
Any vending machine requires periodic refilling, cleaning and cash collection. In the case of coffee vending machines, this is particularly relevant, as running out of water will completely paralyze their operation. In addition, coffee machines require routine maintenance more frequently than, for instance, snack vending machines.
Thus, the vending business’ primary objectives are twofold: firstly, monitor equipment, and secondly, control the operators whose task is to check and service coffee machines.
Coffee vending machine monitoring
Coffee machine servicing can be divided into two parts: routine servicing and technical maintenance. The first one is usually performed once or twice a week — depending on how popular the machine is in the given location. The second one is usually done once a year and entails decalcification of the boiler and hydraulics.
Scheduling routine servicing and maintenance
Since servicing mostly takes place on certain days, you can plan it and build a route in the program in advance. This is where tasks might come in handy: in B2Field you can create both one-time and recurring tasks. Moreover, they are further divided into single tasks (when the vending machine operator needs to visit one specific location, for example, in case of a coffee machine breakdown) and route tasks (for visits to several locations), such as scheduled maintenance of coffee machines.
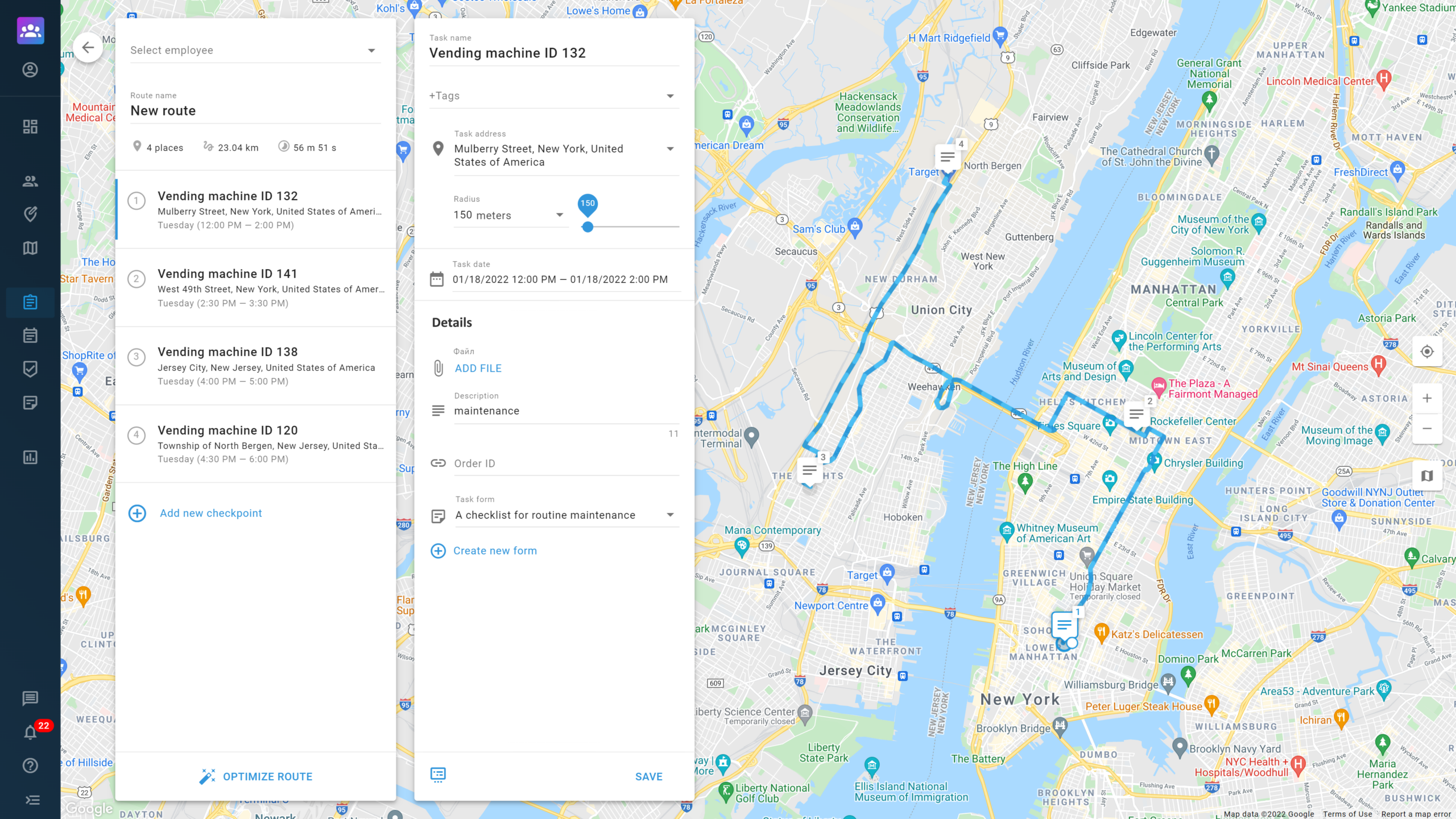
In order to reduce travel time and gasoline costs, use the route optimization tool. Select the locations where the equipment is installed, and the program will automatically build a route, taking into account the remoteness of the objects and the shortest way.
The coffee vending machine operator will receive the to-do list for the day on their smartphone or tablet via B2Field mobile app. This can be done remotely, without dropping by the office. The task will provide detailed information on what needs to be done, and if it is a route task, the operator will receive a list of locations in the order needed for monitoring.
With this task feature in B2Field you can easily control maintenance and be sure to meet all the necessary deadlines by scheduling visits in advance.
Fine-tuning the operators’ work
As we’ve mentioned before, a coffee vending machine requires regular servicing in order for it to function properly and at a full capacity — it’s important not to miss a single step. For this purpose, a checklist can be created in B2Field to monitor equipment performance. It will help the operator to follow instructions while servicing, thereby ensuring continuous operation of the coffee machines, and hence, revenue.
The check-list is created in a mobile form that can be easily adapted to the specifics of a given vending business thanks to the set of multiple features ranging from text fields to an electronic signature. The checklist is available to the operator in a mobile app, where they can tick off what has been done, and transfer this data to the office as their report.
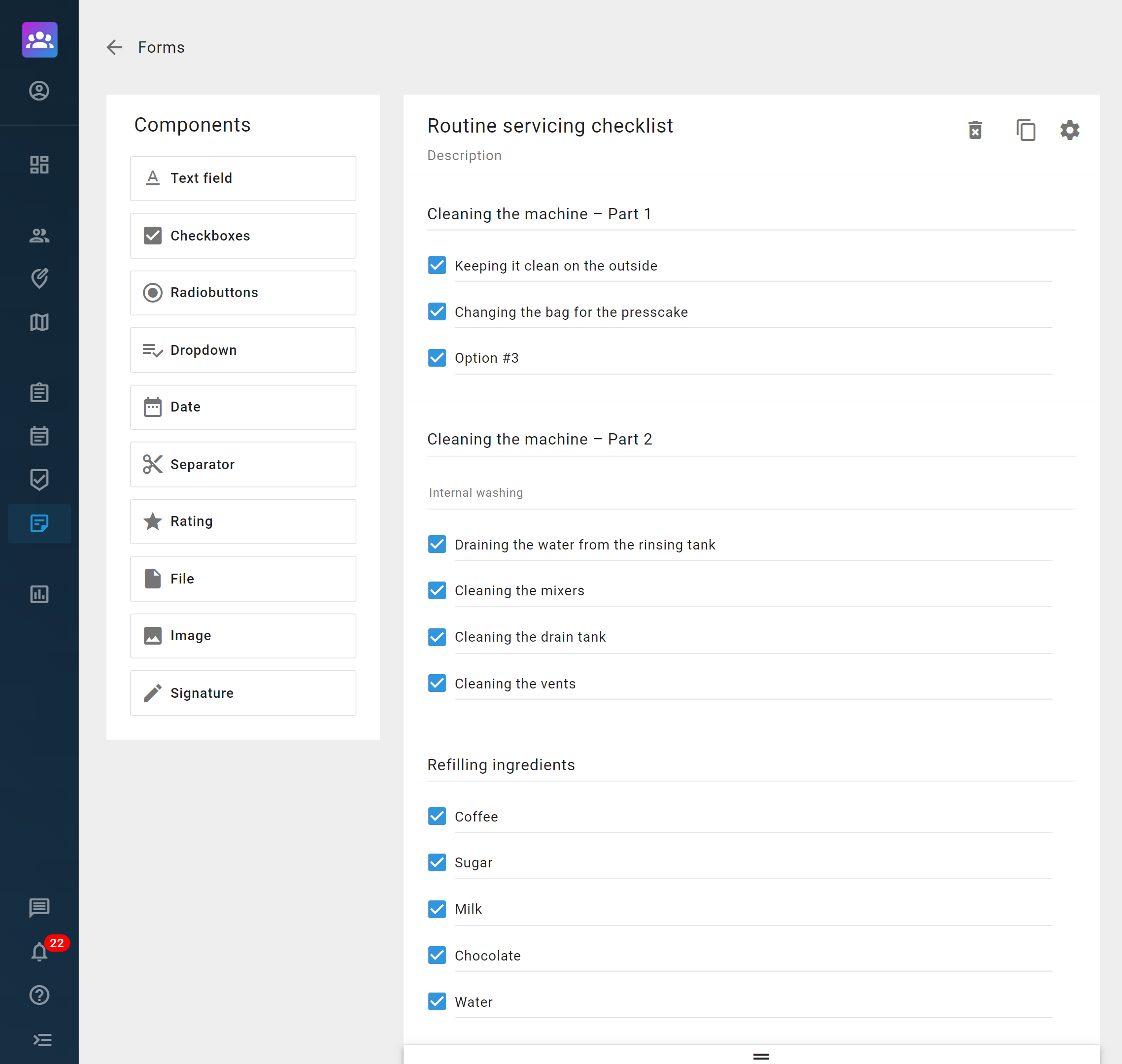
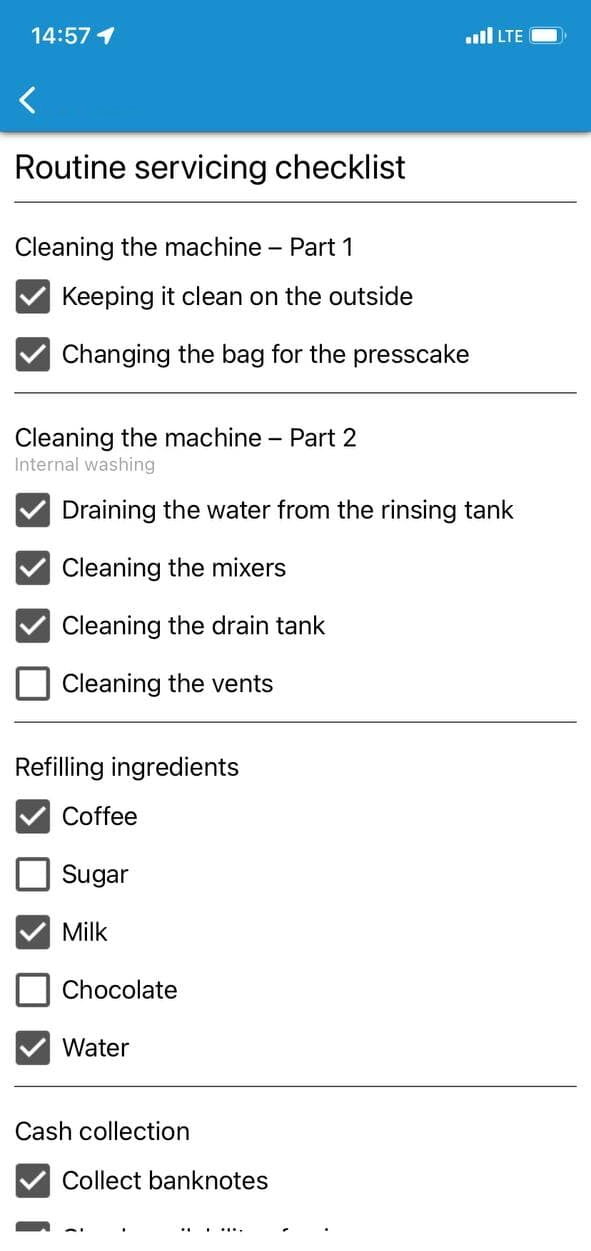
A checklist for routine maintenance in the web interface and app
Supervising the operators
The manager of a coffee vending company needs to know that the coffee machine operator actually completed servicing, otherwise the business would suffer losses. To make sure that the employee arrived on site, you can use photo reports and a GPS tag with the time, date and address.
As soon as the operator arrives at the location, the supervisor will get a notification in their B2Field account. What’s important is that the employee’s mobile app records the length of time they have stayed at the task location, which means the supervisor can check how long it took the operator to complete the servicing. On average, routine servicing takes 40 to 60 minutes, so if an operator has completed a task too quickly and reported for full maintenance, it might be a good idea to monitor them more closely.
It is also very convenient for the operator to fill out reports in a mobile form via the B2Field app. Once completed, the form will be sent by the operator and can be immediately checked in the office.
Statistics for seamless operation
The data collected through mobile forms is easy to analyze as the information is structured and stored electronically. Therefore, you can easily find out how often a particular coffee machine needs to be serviced on a regular basis. This way you can reduce downtime or, on the contrary, minimize costs by decreasing the frequency of visits.
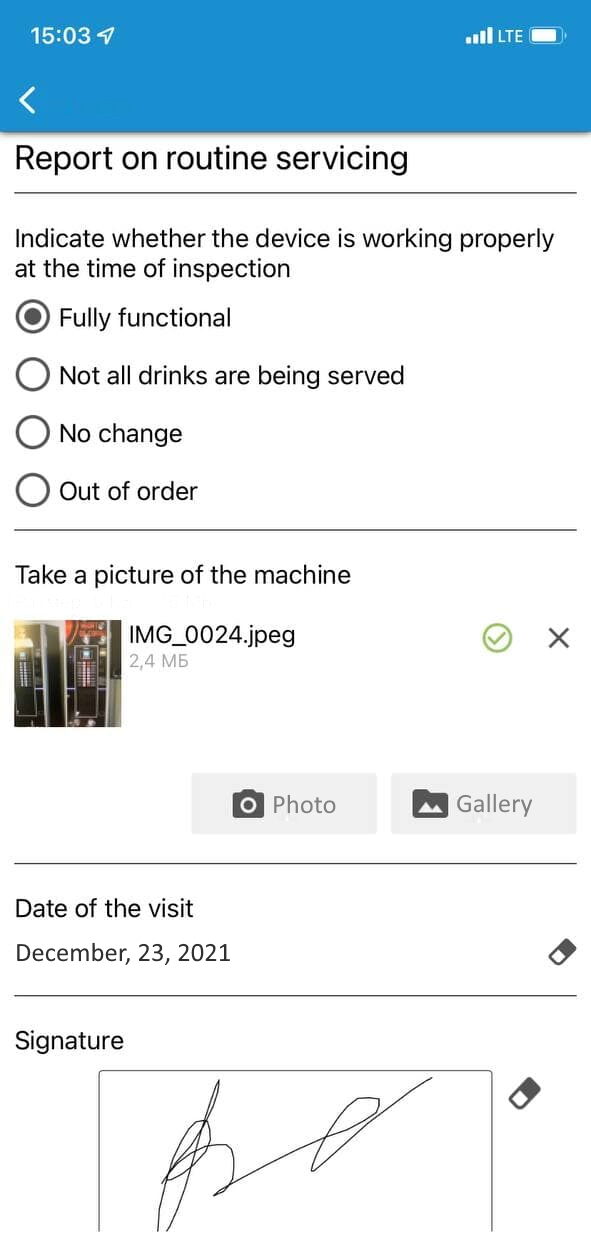
Along with equipment performance data analysis, with B2Field you will be able to evaluate coffee vending machine operators’ productivity: the number of tasks completed, travel time and time on the job, as well as keep track of their working hours.
Thus, using the B2Field web service and mobile app you can monitor both your coffee vending machines and operators’ performance. By collecting and analyzing data, you can easily find growth points and adjust business processes to help you earn even more.